Case Study - CodeVerify
In-line Barcode Verification System
INTRODUCTION
Mislabeling in the food manufacturing industry can result in costly recalls, regulatory penalties, and damaged brand reputation.
For a global food manufacturer in Kentucky, labeling errors were a persistent challenge due to manual processes and frequent changeovers.
To address these issues, we implemented the CodeVerify In-line Verification System, a high-speed automated solution that scans and verifies every label in real-time (up to 350 ppm), ensuring 100% label accuracy before application.
By automating the verification process, the system eliminates human error, reduces waste, and improves production efficiency.
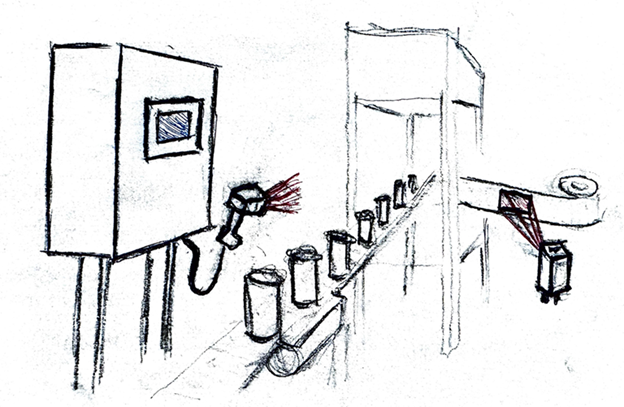
Executive Summary
Incorrect label placement and selection are common issues in high-volume manufacturing, leading to operational disruptions, regulatory risks, and damage to brand reputation. These errors often stem from manual processes like operator setup mistakes and changeovers, where human error can go undetected due to inconsistent checks.
Examples of labeling problems include applying the wrong label, such as swapping brand labels, or missing labels entirely. In the food industry, these issues can result in regulatory non-compliance, costly recalls, and increased waste in production.
Operator retraining is a common solution to address labeling errors. It helps reinforce best practices and closes knowledge gaps, improving employee understanding of procedures and quality standards.
However, retraining alone may not fully resolve the problem. Human error is unavoidable, and without automation or error-proofing techniques, errors may persist. Retraining also requires time and resources, which could be better invested in process improvements or technological upgrades.
When labeling issues are rooted in systemic problems like outdated equipment or poor workflow design, retraining cannot address the underlying causes. Additionally, frequent retraining can lead to employee fatigue, diminishing its long-term effectiveness.
GOAL and OBJECTIVES
Enhance label accuracy and confidence by implementing strict quality control measures during the production process. Error detection just before the point of application can help correct errors early and just in time, reducing the likelihood of labeling mistakes.
Proposed Solution: Inline Barcode Verification System
To address the issue of mislabeling effectively, an inline barcode verification system is proposed as a key preventive measure, complemented by operator retraining where necessary. This system provides a high-speed, automated solution that ensures every label is correct before application, significantly reducing the risk of errors while simplifying operations.
How It Works
The inline barcode verification system is designed to scan and verify barcodes on labels as they enter the application area. The process requires minimal operator input beyond selecting the desired match code for the production run. This selection sets the standard barcode against which all incoming barcodes are checked, with mismatches flagged immediately and prevented from proceeding.
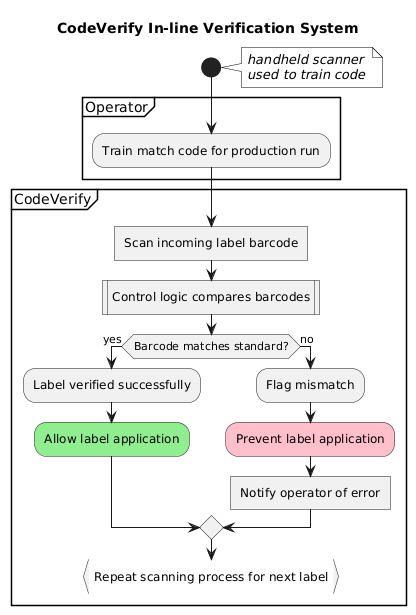
Key Features:
- High-Speed Verification: Capable of scanning every label without slowing production.
- Automation-Driven Accuracy: Ensures consistent performance by removing reliance on manual checks.
- Ease of Use: Operators can quickly set and modify match codes through an intuitive interface.
- Error Mitigation: Prevents incorrect labels from being applied, reducing waste and scrap product.
PROJECT SCOPE
Hardware Setup
- Design and produce the industrial control panel for electrical connectivity and component housing.
- Install barcode scanners with appropriate mounts for optimal positioning.
- Integrate scanners with the Quadrel labeling system, ensuring physical alignment for accurate barcode reads.
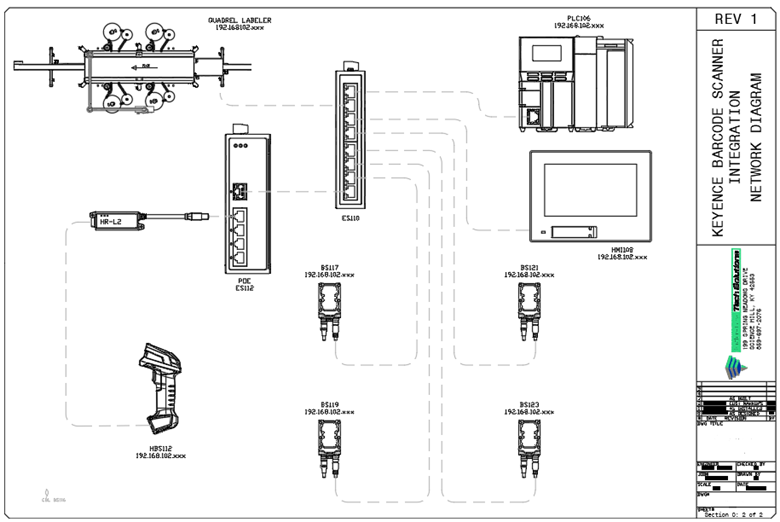
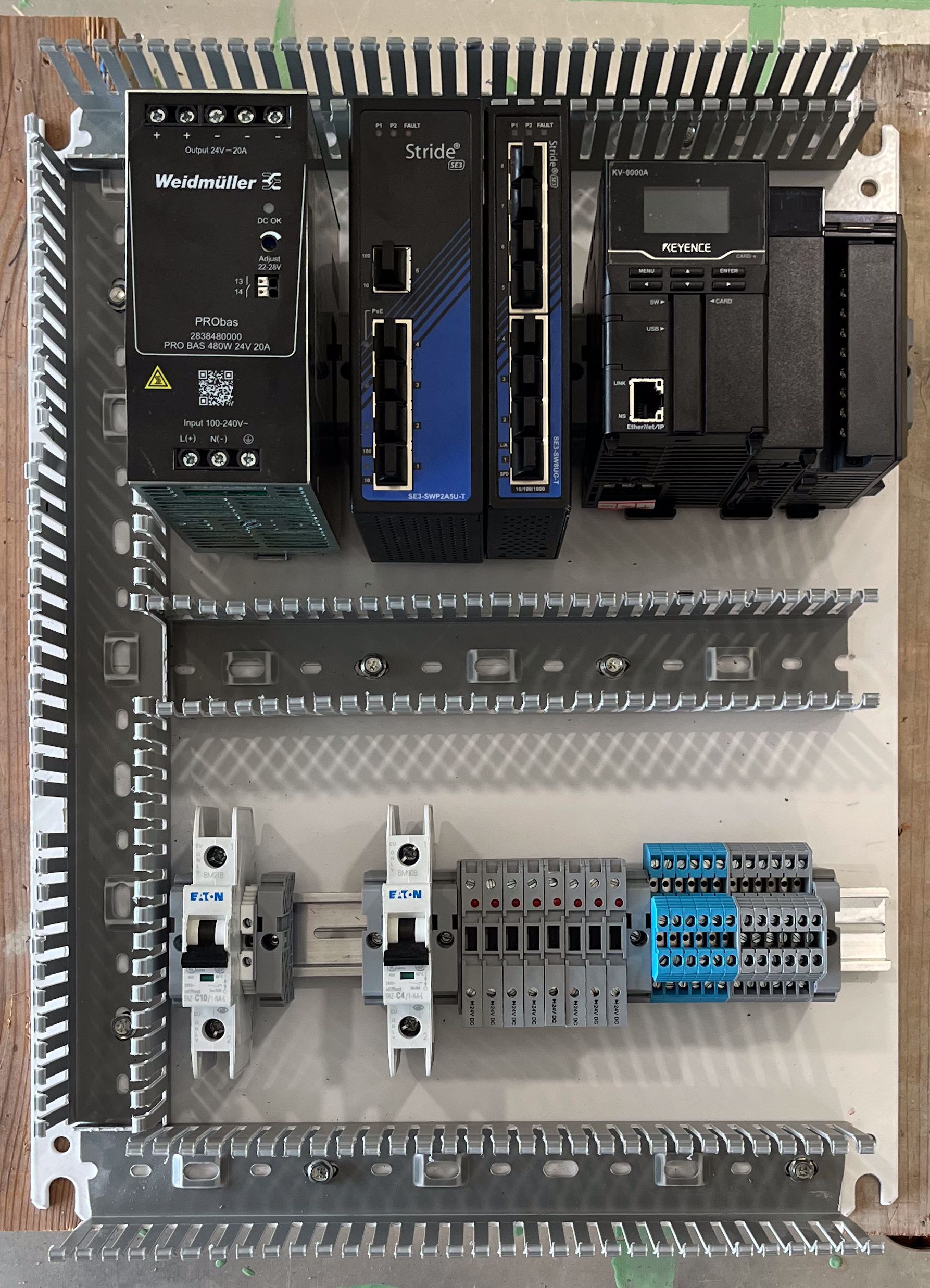
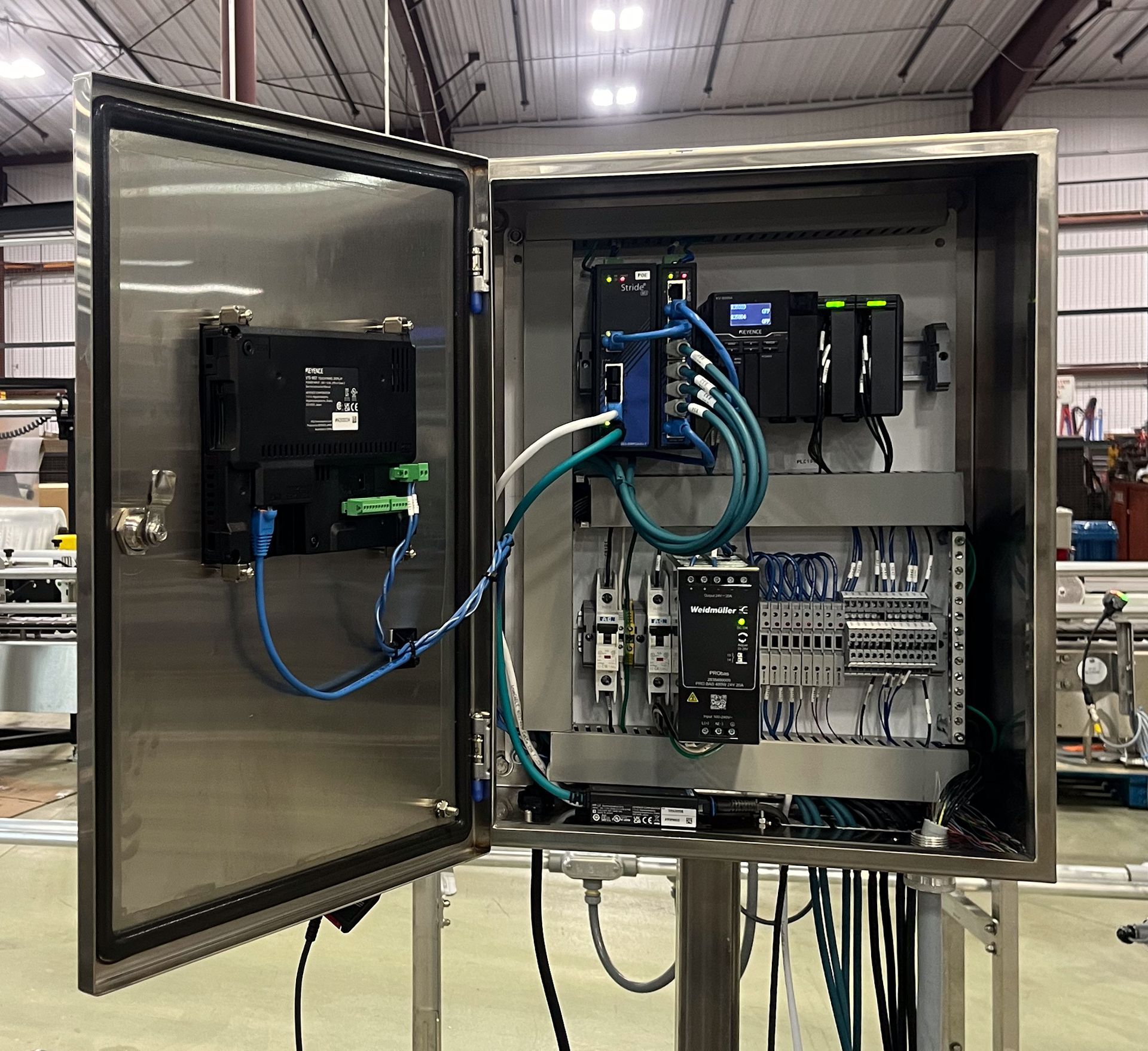
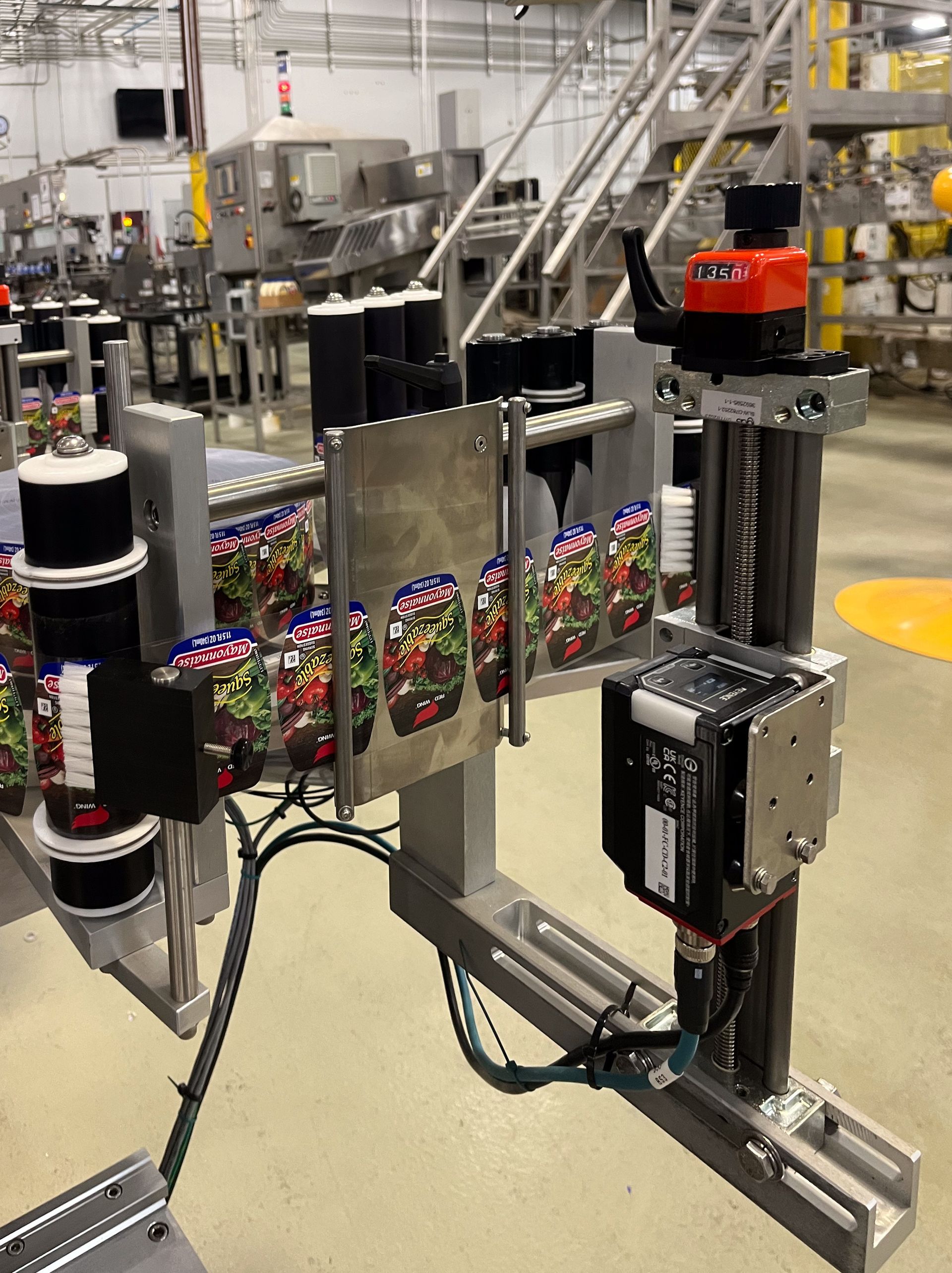
Electrical Design: Develop wiring diagrams, specify components, and ensure proper integration of PLCs, scanners, HMI, and related hardware into the system.
PLC Programming: Configure devices, implement FIFO logic for barcode data, develop match/fail verification, and integrate control with Allen-Bradley CompactLogix.
HMI Programming: Design intuitive screens for monitoring, operation, and alarms, dynamically linked to PLC data.
Testing & Debugging: Validate scanner accuracy, debug barcode comparison logic, fine-tune scanner settings, and test system communication with labelers and barcode systems.
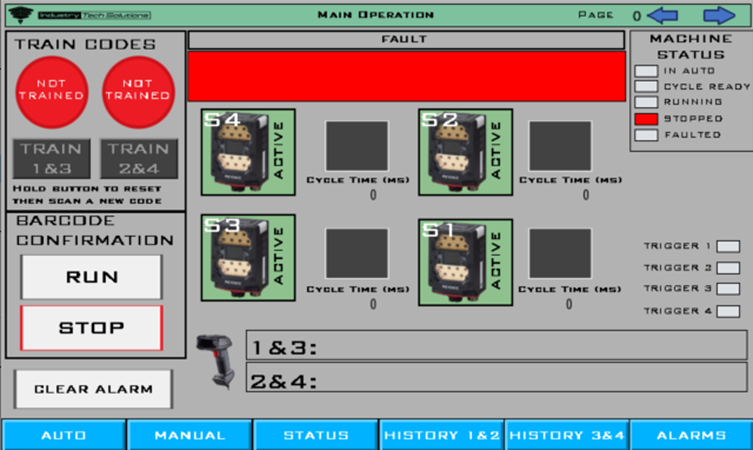
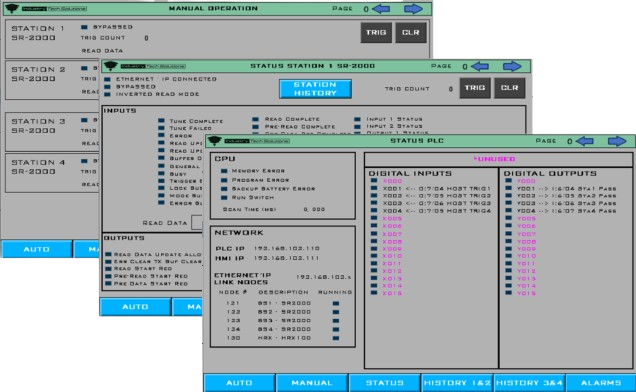
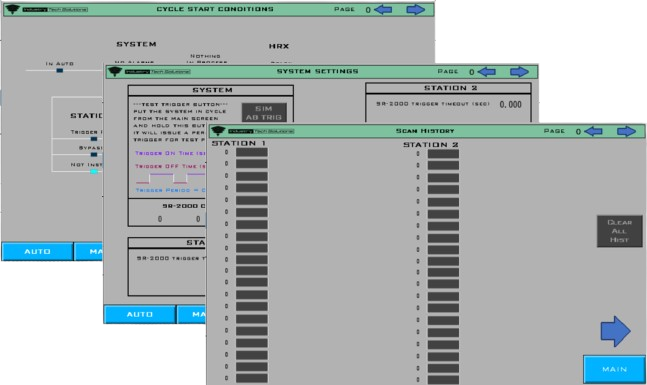
RESULTS
The fully integrated inline barcode verification system was successfully installed and integrated seamlessly with the functionality within the Quadrel ProLine Labeling System. The system met the high-speed operation requirements of 350 bottles per minute. Below is a detailed overview of the deliverables, integration, performance tuning, system operation, and its overall impact.
The project deliverables included:
- A fully integrated inline barcode verification system with automated match/fail detection capabilities.
- Functional and intuitive HMI screens for system operation and real-time monitoring.
- Comprehensive project documentation, encompassing programming code, network configurations, and detailed system operation manuals.
Integration and Timing Optimization
To ensure optimal performance, the barcode verification system was tightly integrated with the Quadrel labeler via physical I/O connections.
Key optimization steps included:
- CompactLogix RPI Adjustment: The Requested Packet Interval (RPI) on the Allen-Bradley CompactLogix controller was fine-tuned from the default 10 ms to 1 ms, enabling high-frequency signal processing.
- Keyence PLC I/O Optimization: The input time constant on the Keyence PLC's I/O card was reduced to 1 ms as well, facilitating operation at the line's maximum speed of 350 ms per cycle.
This change allowed the system to handle the line's maximum speed of 350 ms per cycle effectively.
Scanner Performance
The barcode scanners underwent extensive fine-tuning for both 1D and 2D barcodes:
1D Barcodes: Decode times were optimized to 35-45 ms.
2D Data Matrix Codes:
Decode times ranged between 60-90 ms.
The system maintained a total timeout of under 170 ms, including internal processing.
System Operation
Barcode Verification Logic: The system ensures a "pass" for correctly matched labels or a "fail" for missing/timeout or mismatched barcode.
Operator Workflow: The Keyence HR-X100 handheld scanner allows the operator to train the master barcode for front and rear labels based on a provided job sheet.
After training, the operator manually triggers the inline scanners to verify proper label positioning
Once verified, no additional setup is required until a new production job begins or a new code is retrained.
Impact
The system effectively prevents issues caused by misloading incorrect label types during reel changes reducing labeling errors:
Operators found the system intuitive and required minimal retraining to adapt to the new workflow.
The system's operation and usability have allowed the operators to gain confidence in the system and utilize it daily in production runs.
If you believe that the CodeVerify In-line Verification System could solve similar labeling challenges at your facility, we encourage you to reach out to us at Sales@industrytechsolutions.com or 859-679-2076. If this case study has sparked your interest in working with Industry Tech Solutions for a different automation project, we would be happy to discuss your needs and explore how our solutions can help optimize your operations.
ADDITIONAL BACKGROUND AND COMMENTS
Incorrect label placement or selection is a common issue faced by manufacturers, particularly in high-volume environments. Mislabeling can occur for several reasons and carries significant risks, including operational disruptions, regulatory non-compliance, and potential damage to brand reputation.
Causes of Labeling Errors
The root causes of labeling errors often stem from manual processes in the production line, including:
- Operator Setup Errors: Manual selection of the wrong label roll or misconfiguration of labeling equipment can lead to incorrect labels being applied.
- In Process Changeovers: Swapping label rolls introduces the risk of human error.
Inconsistent manual checks or missing verification steps can allow mislabeling to go undetected.
Examples of Labeling Issues
Wrong Label Application: Instances where products intended for one brand are mislabeled with another brand’s packaging or where front and rear labels are swapped.
Missing Label Application: Rare cases where labels are missing from the web or are not applied at all during production.
Repercussions of Mislabeling
Incorrect product labeling in the food manufacturing sector has several negative consequences:
- Regulatory Non-Compliance: In the food industry, regulatory bodies require accurate labeling, particularly for allergen disclosures. Labeling errors that misrepresent allergen content or nutritional information can lead to non-compliance with FDA or similar standards.
- Large-Scale Recalls: Labeling errors often result in costly recalls. Undeclared allergens are a common cause, posing health risks to consumers and financial risks to manufacturers.
- Example: In December 2024, a major confectionery company recalled cappuccino-flavored bars due to missing allergen warnings for tree nuts.
“The recall was initiated after it was discovered that the tree nut-containing product was distributed in packaging that did not reveal the presence of tree nuts. Subsequent investigation indicates the problem was caused by a temporary breakdown in the company's production and packaging processes”.1
- Example: A beverage manufacturer voluntarily issued a recall of thousands of cases of beverages mislabeled with incorrect sugar content, posing potential health risks for individuals managing diabetes.
“[beverage manufacturer] has recalled more than 13,000 cases of [beverage] because the mislabeled cartons actually contained the full-sugar version of the drink, according to a report2 from the US Food and Drug Administration.”3
- In-House Waste and Scrap: Labeling errors contribute significantly to scrap rates within production facilities. While specific data varies, such errors can result in waste rates exceeding industry benchmarks.
One study4 conducted by NiceLabel (now owned by Loftware), a label design and printing software company, indicates that U.S. manufacturers incur average losses of approximately $1.17 million annually due to production line shutdowns caused by label printing issues. 67% of manufacturers experience production line shutdowns exceeding one hour when label printing problems occur, with an additional 21% facing shutdowns lasting more than 30 minutes. Manufacturers pause production lines nearly six times per year on average due to labeling issues.
Another survey5 , conducted by Packaging World magazine and sponsored by Digimarc Corporation, shows that for manufacturers that monitor label accuracy, 80% will report a problem from mislabeled products on their primary production line.
Operator Retraining in Addressing Labeling Challenges
Operator retraining is a common response to incidents involving incorrect label placement. While it can address immediate concerns and provide preventive benefits, retraining alone is often insufficient to resolve the broader challenges of labeling accuracy.
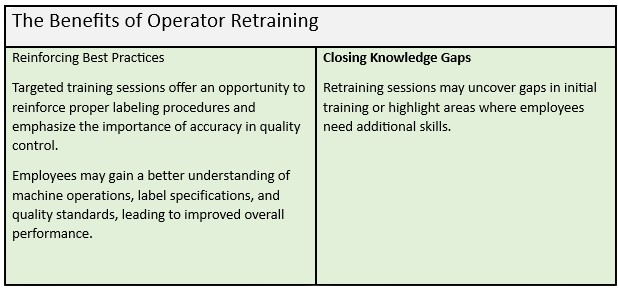
Ultimately, retraining provides a structured avenue to address issues immediately following an incident providing a prompt corrective action
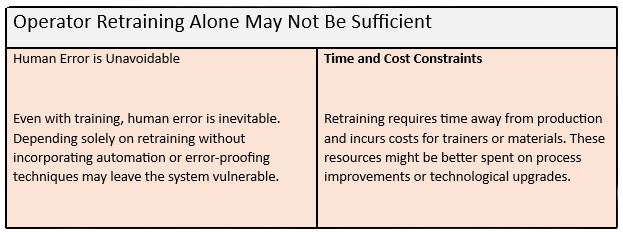
However, retraining focuses on human performance, but the root cause might be systemic, such as outdated equipment, poor workflow design, or lack of automation. In such cases, retraining will not solve the underlying problem. Frequent retraining sessions can lead to fatigue or resentment among employees, reducing their effectiveness over time.
References
2. https://www.accessdata.fda.gov/scripts/ires/?Product=209972
3. https://www.cnn.com/2024/10/16/health/coca-cola-recall-minute-maid-zero-sugar-lemonade/index.html
5. https://www.digimarc.com/press-releases/2019/09/26/new-survey-reveals-80-percent-manufacturers-mislabel-products-annually